Our Product Line
Solving Fuel & Oil Contamination Challenges
Smart Filtration Kits
Smart Filtration Kits are designed for ease of installation & service and come with our Ultra High Efficiency Filters that fit on our cast aluminum filter heads to accept high flow rates and extend service life.
Our Ultra High Efficiency Filters are designed with Donaldson’s proprietary synthetic media to remove 99.98% of abrasive particulates in a Single Pass. Inside our filters, Donaldson’s innovative filtration technology allows high dirt holding capacity, low initial differential pressure, and Ultra High Efficiency Single Pass Filtration. All our filters are equipped with Viton seals to have optimum compatibility with various fuels and oils.
Smart Filtration cast aluminum Filter Heads with steel inserts prevent excessive metal-to-metal friction and adhesion between the head and the filter. Our Dual Filter Heads are designed for parallel flow for the lowest pressure drop while providing Ultra High Efficiency Single Pass Filtration.
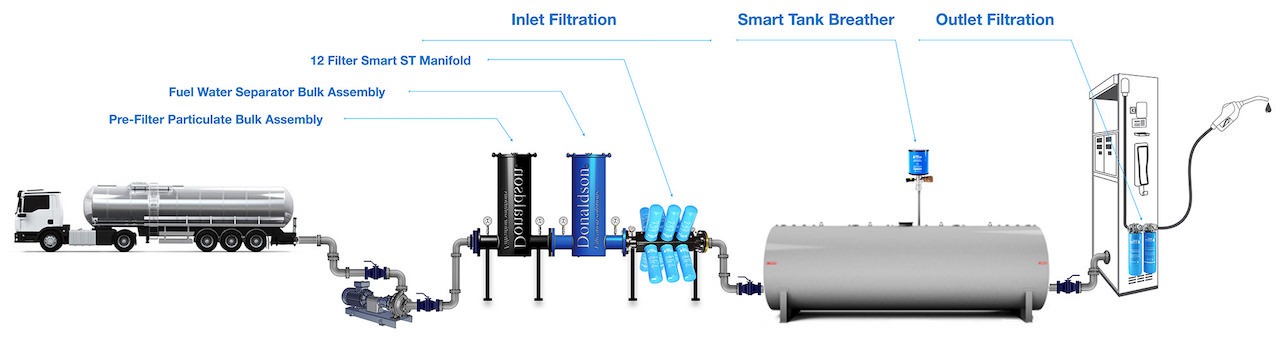
Standard Smart Filtration Kit
For flow rates up to 65 GPM / 246 LPM
The Standard Smart Filtration Kit is perfect for smaller operations that need clean fuel delivered efficiently in any environment.
Kit Contents:
- Single Filter ST Head
- 4μm ß5000 ST Filter with D.E.R.T
- Pressure Gauge Adapter
- Pressure Gauge
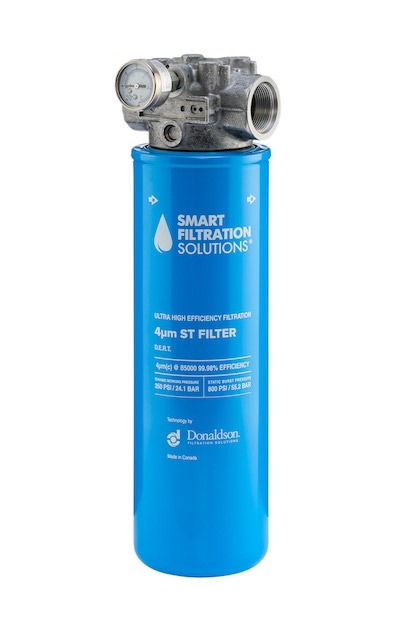
Clean & Dry Smart Filtration Kit
For flow rates up to 50 GPM / 189 LPM
The Clean & Dry Smart Filtration Kit removes fuel contamination, stops water as it leaves the bulk tank.
Kit Contents:
- Two Single Filter ST Heads
- 4μm ß5000 ST Filter with D.E.R.T
- Water Absorbing ST Filter
- Two Pressure Gauge Adapters
- Two Pressure Gauges
- Connecting Nipple
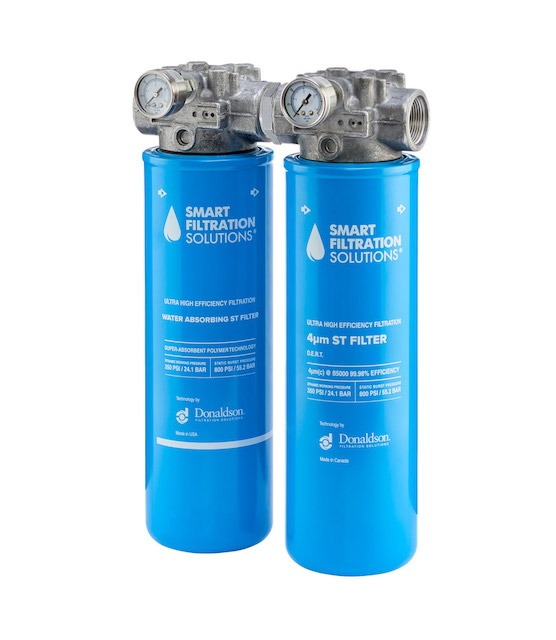
High-Capacity Smart Filtration Kit
For flow rates up to 125 GPM / 473 LPM
The High-Capacity Smart Filtration Kit works for operations with high- flow delivery systems that regularly need large quantities of clean diesel delivered efficiently.
Kit Contents:
- Dual Filter ST Head
- Two 4μm ß5000 ST Filter with D.E.R.T
- Water Absorbing ST Filter
- Pressure Gauge Adapter
- Flange Adapters
- Connecting Bolts
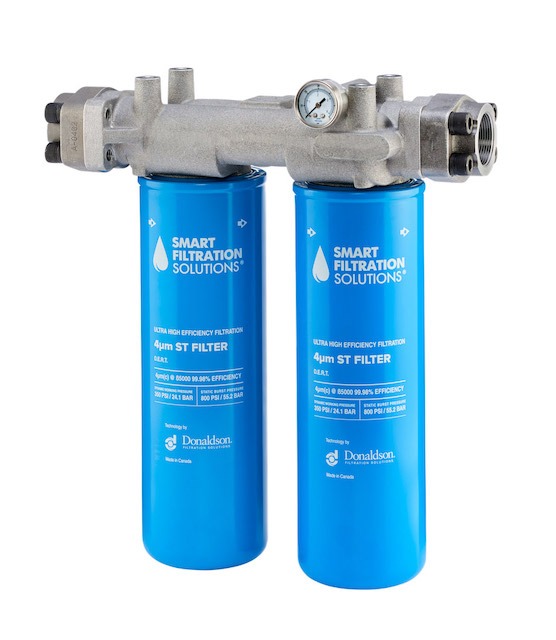
Modern Engines Demand Clean Fuel
Progressive introduction of increasingly stringent emission standards have resulted in sophisticated diesel engines that require cleaner fuel than ever before to operate efficiently, due to injection pressures of more than 30,000 PSI and extremely tight tolerances. In engines where precision is everything, you can’t risk the damage done by high-velocity microscopic contaminants. At 30,000 PSI (2000 BAR), every unfiltered particle acts almost like a tiny sandblaster, eroding the injector, creating inefficient spray- patterns and potentially over-fueling the engine. A fouled injector doesn’t spray fuel efficiently and may lead to improper idle, irregular fuel distribution, unsuitable exhaust emissions and poor fuel economy.
We Have Great Answers
Frequently Asked Questions
Common rail injector’s pressure can go up to 2700 BAR. This increase in pressure has a major impact on the cleanliness level of the fuel that is allowed to flow through the injector.
We always stress the fact that the main aspect to consider in choosing a filtration unit is the balance of efficiency, capacity and pressure drop. There are many factors to consider when it comes to dirt holding capacity: flow, viscosity, system pressure drop, contaminant properties, etc. All these factors have an impact on the dirt-holding capacity of a filter.
If you get a bad batch of fuel, a kidney loop system will then have to recirculate the entire volume of what was in your tank + the new delivery. A kidney loop system cannot physically clean all fluid in the tank; there is always a point of zero gravity that a kidney loop system will not filter. Start – Stop principle that is frequent at a kidney loop releases small particles.
As long as tanks are interconnected and have one main inlet, it doesn’t matter how many tanks you have on site. We carefully design and size up the installation to coup with service intervals. Some of our end users have up to 8 fuel tanks connected to a single manifold on the inlet side.
Smart Filtration Solutions gives you 100% control over the cleanliness of fuel you receive. Many people assume they are buying quality fuel that meets the required specifications; diesel fuel cleanliness is rarely questioned. But higher fuel systems operating pressures, lower system tolerances and tighter filtration have pushed fuel cleanliness into the maintenance spotlight.
Normally, laser and automated white light particle counters are used to detect the contamination that is present in fluids. It may happen that these particle counters are not accurate and count phantom particles because of the difficulty in differentiating dirt, water or additives. Phantom particles count is more present in fluids blended with additives than in base fluids.